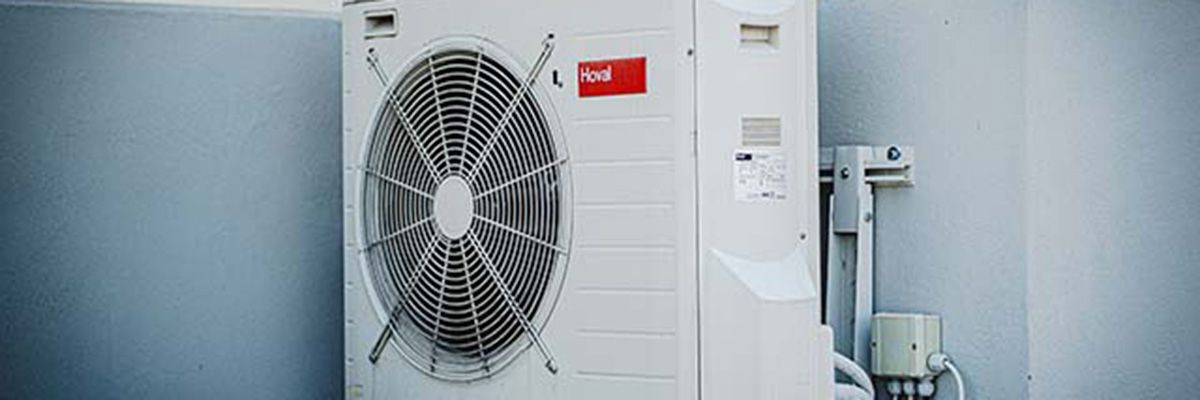
How do variable frequency drives reduce energy consumption for your business?
Reducing energy is now a pressing concern for all businesses and a simple change can make a big difference – the introduction of variable frequency drives. Research by the International Energy Association suggests that electric motor-driven systems (EMDS) account for more than 40% of global electricity consumption. In theory, this is good news for facilities that are pressed to cut energy costs in a climate where they’re rapidly spiraling in the wrong direction, upwards.
Why good news? Because EMDS, run effectively, hold the potential for dramatic savings to be achieved. The IEA projects that as much as 25% of the electricity they generate could be cost-effectively eliminated and this, in turn, would cut total global electricity demand by about 10%.
We may now be reaching an inflection point where, though the issue of the energy efficiency of EMDS has heretofore been somewhat neglected, market conditions in the present commercial landscape will ensure that doesn’t remain the case for long.
With the need for prudent financial management to the fore in a difficult economy, resources are likely to be committed to realizing the vast savings potential of optimized EMDS. How, then, can energy consumption be reduced? How does the technology work?
Variable speed drives save energy
The answer is through a variable frequency (or speed) drive, which is installed to control a motor’s speed and torque.
Technologies that do this don’t come as standard. Generally, motors are designed and built to rotate only at a set speed. This (speed) is broadly determined by the number of magnetic poles built into the motor along with the supply voltage and frequency applied.
Motors cannot inherently alter their speed despite the reality that the different applications they power perform optimally at different speeds. Energy, therefore, is wasted each time a motor rotates at a sub-optimal speed for a designated application. In industry, this wastage is far from uncommon.
Control voltage and frequency to reduce costs
To address the problem, enter the variable frequency drive. In rough terms, VFDs are a technology that enable effective speed control of AC motors by manipulating voltage and frequency. Doing so provides consumers (facilities managers, building managers, etc.) with improved process control, reduced wear on machines, increased power factor and often sizable energy savings.
While the benefits above are universal, the question of how the VSD technology works to accrue them is specific to the type of underlying application. This is usually defined by its torque category.
Most applications fit into one of the following:
- Constant torque load applications: These applications demand a starting torque rate proximate to the rated torque of the motor. As a result, as they approach rated speed little change is required. Conveyors are one example of a constant torque load application.
- Linear torque load applications: These applications have a more consistent, straight-line torque requirement that increases proportionately with speed. Screw compressors are a good example here.
- Variable torque load applications: These torque requirements of these applications increase proportionately with the square of the speed and reach 100% torque just below rated speed. Fans and pumps are common examples of variable torque load.
It’s in the latter category (variable torque load) that variable frequency drives can be used to generate significant energy savings. That’s because the relationship between speed and power results in energy savings of 50% when a fan’s speed is reduced by only 20% (for the mathematically inclined reader, the reason this is the case is Cube Law). The takeaway here is that for most motion control applications, controlling motor speed by deploying a VSD quickly delivers sizeable energy savings and, in turn, benefits the bottom line.
Variable speed drives – VSDs- deliver across the board
There are other paradigms through which savings can be accrued through the greater control of the motor delivered by the variable frequency drive. Briefly, these include:
- Square law fluxing: Altering the speed of variable torque loads can deliver power savings proportional to a fraction of the speed reduction because in variable torque applications, there is always unused torque capability available. When linear voltage is adjusted to frequency relationship, torque capability of the motor is reduced, in the process reducing energy losses.
- Dynamic V to F mode: For applications where power loss in the motor needs to be kept to a minimum under low load conditions a VSD will vary the voltage it applies to the motor depending on load level, so the motor is reduced when load levels don’t require full capacity. This reduces losses in the motor itself.
- PID control: Here, AC drives vary the speed of the motor to match the effort required by an application resulting in considerable savings in energy consumption. This is achieved using a closed-loop regulator and is often found in motors related to powering pressure, level, and temperature control.
- Active Front End Systems (AFE): These systems employ a controlled rectifier bridge which allows energy to flow in both directions between mechanical system and AC supply. This result is far greater efficiency levels in applications where electrical braking would otherwise be required, which results in significant amounts of energy being wasted as heat.
Time to act: next steps to leverage the variable frequency drive opportunity
If you’re interested in learning more about how variable frequency drives can help your enterprise reduce energy costs, please send an email to:
We’d be happy to talk you through the advantages of the technology in greater detail.
At NexRev, we’ve been unlocking the power in facility and energy management data with over half a million connected devices across North America. Our team of experts is focused on helping you deliver more with your budgets, infrastructure, and assets to create sustainable savings in operations and energy, reducing your risk and increasing operational confidence – and boosting the bottom line.